It's been six years since I reported in Rod & Custom about a 1960 Thunderbird custom project underway based on some Eric Black illustrations that had appeared in R&C the previous year. That project never took off, but the illustrations managed to inspire another second-generation T-bird enthusiast. Now a slight variation of Black's original concept is under construction at Hollywood Hot Rods (HHR). Most of the sheetmetal modifications (including the chopped top and reshaped fins) are very subtle, but required an extensive effort to achieve. On a stock body, the spears lose their shape once they get past the rear wheel openings, widening to match the bumper. Altering that to match Black's design involved an extensive amount of reshaping to the quarter-panels and the rear bumpers. Take a look at the amount of work involved in extending this fabulous Thunderbird's side spears all the way back to the bumpers.
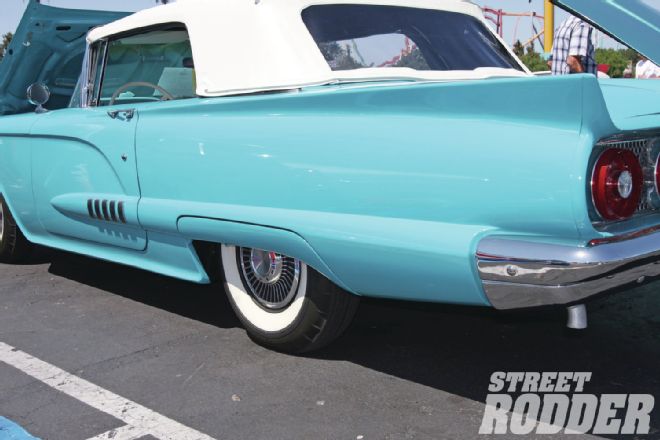
1. On an unmodified 1958-60 Thunderbird, the quarter-panel spears widen out at the bottom at the rear of the wheels, and the lower body shape disappears altogether.
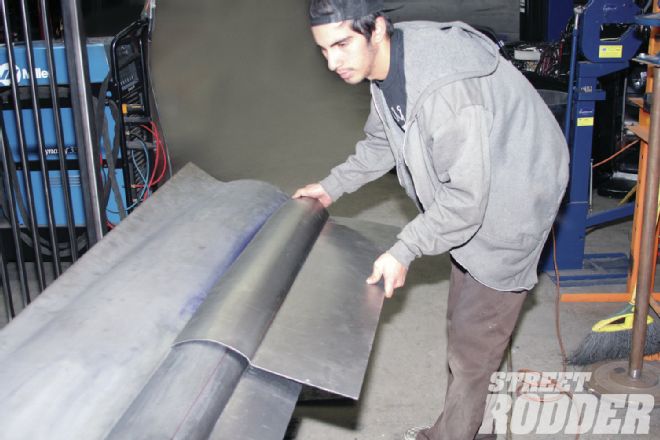
2. Figuring out how to extend the spears, lower the body lines, and reshape the wheel openings was the challenge facing HHR fabricator Mychal Fierro. He bent a piece of 20-gauge steel (the same as the stock quarter) on the brake and used a slip roll to create the initial arc of the spear.
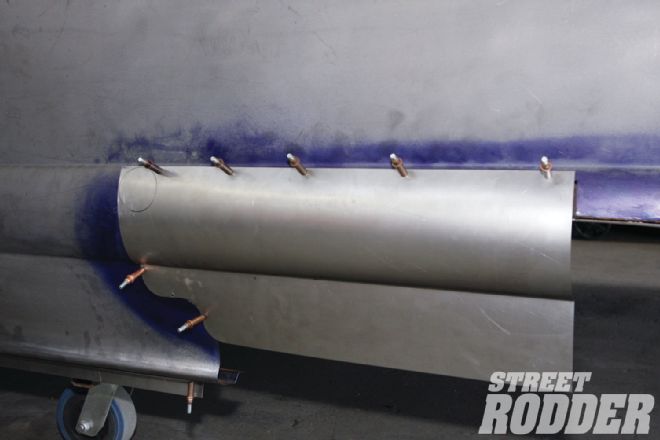
3. The quarter-panel above the spear is fairly flat near the door and much more rounded at the rear. In order to maintain this same shape below the spear, the curve of the spear has to get progressively deeper as it moves farther back.
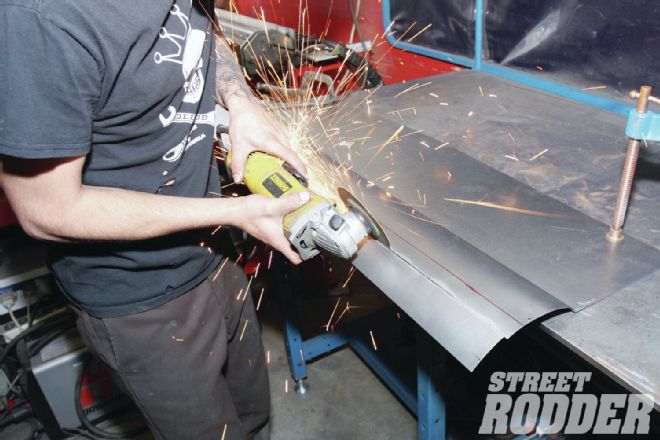
4. The top edge of the replacement panel was measured and cut where it will be welded to the original sheetmetal.
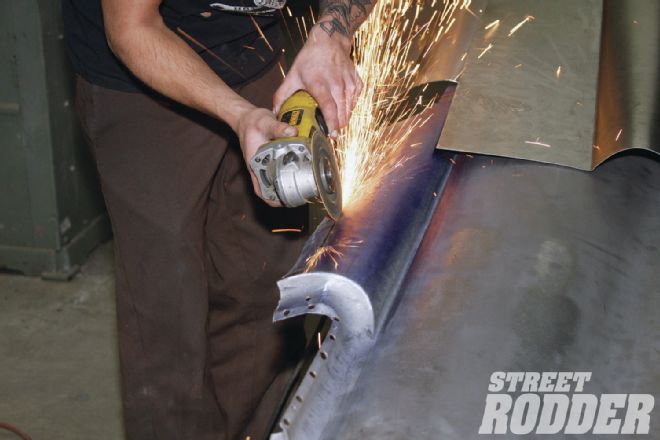
5. The lower portion of the original spear was also cut where the weld will be. The spear shape in the quarter stops before reaching the end of the body (arrow). The shape is continued by the wrap-around bumper.
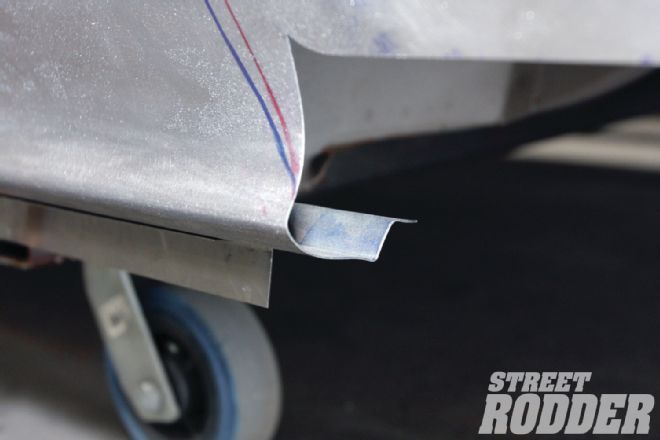
6. Just to keep the job complicated, the lower portion of the factory quarters have a concave shape running into a lip, which ends at the front of the wheel opening. The lip will be extended on this car and will taper out.
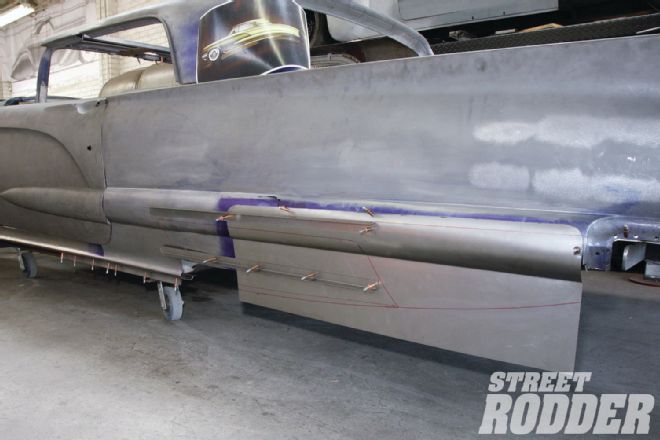
7. This custom panel shows the early stage of the extended spear. There is enough sheetmetal below the spear to continue the lower body lines. The marked lines on the panel (arrows) show the location of the wheel opening and the curve of the lower body.
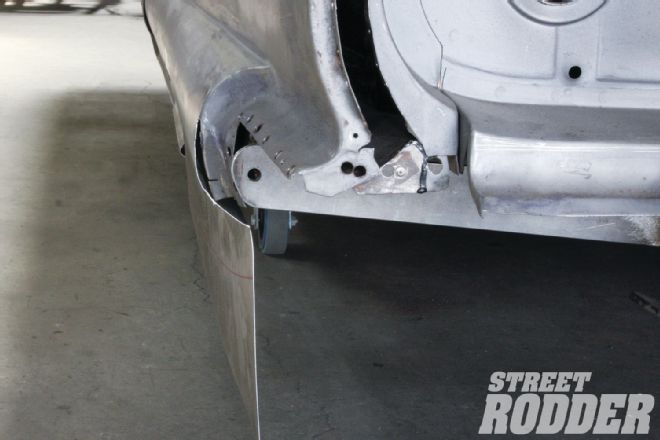
8. From the rear, the arc of the spear and the changing curve of the quarter-panel are easy to see.
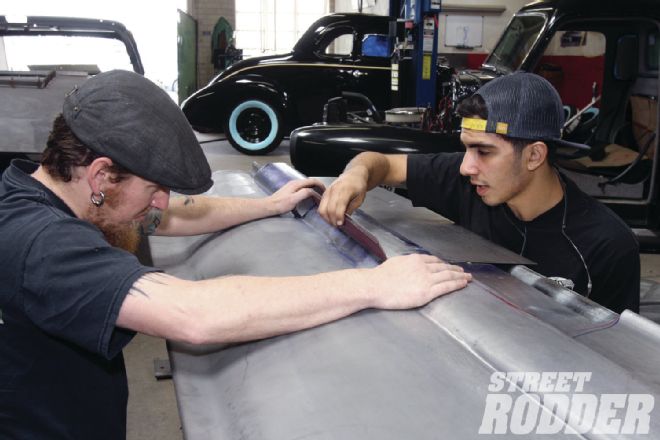
9. Notice how the arc of the spear is much shallower at the front (lower right) than at the rear. Constant measuring plus lots of hammer and dolly work was needed to keep all the different contours looking smooth.
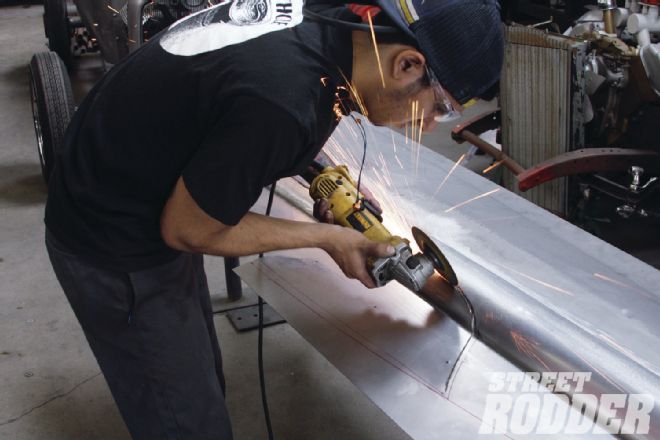
10. After the new lower quarter-panel was welded in place and metal finished, the new wheel opening was cut. Once again, notice how deep the rear of the extended spear is, making the surfaces above and below the spear aligned.
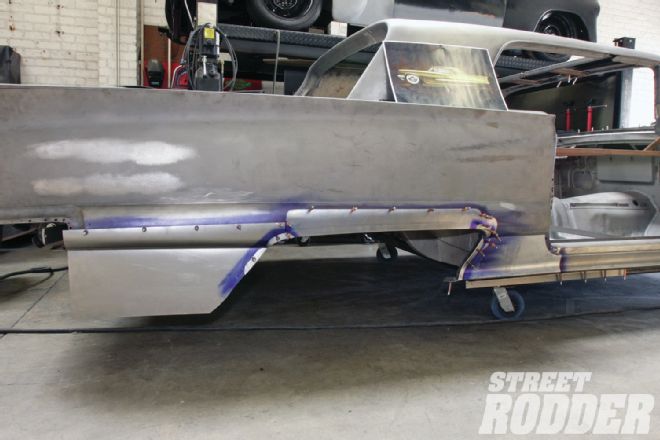
11. The new wheel opening was intended to match the angle of the roof pillars. Added sheetmetal brings the upper edge of the opening approximately 2 inches lower than stock.
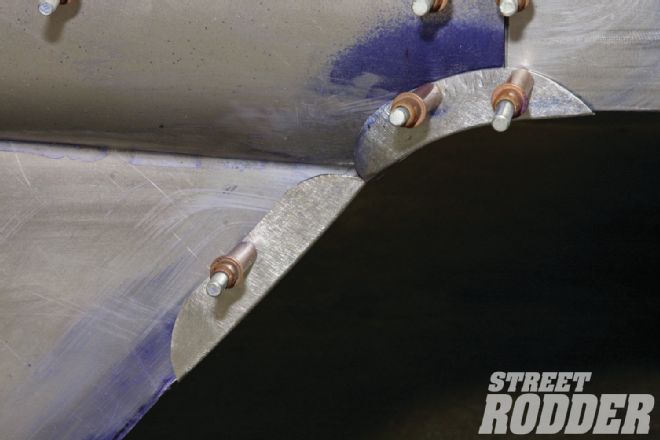
12. It was necessary to use numerous small pieces of sheetmetal to create the right shape and match the multiple angles and curves in the panel.
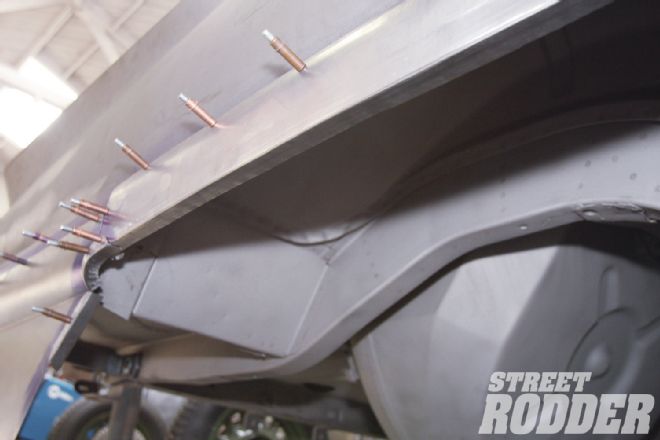
13. The perimeter of the wheel opening was finished with a 3/4-inch flange.
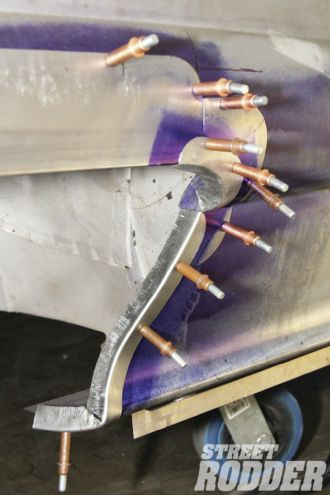
14. The front of the opening was an especially involved process, using numerous small pieces of sheetmetal.
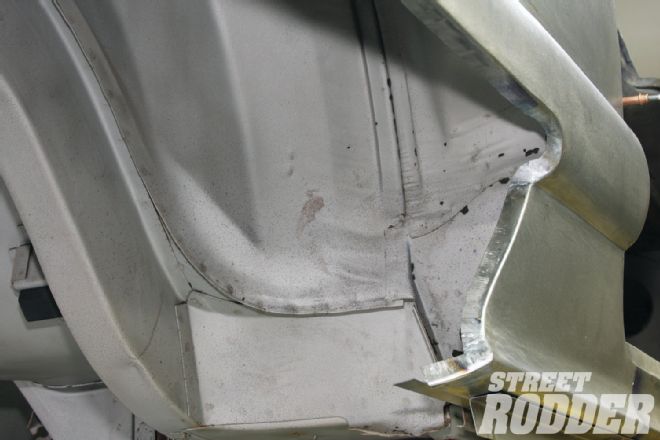
15. You can see how the section below the spear shifts from convex to concave in a mild S shape, finishing with the lower lip.
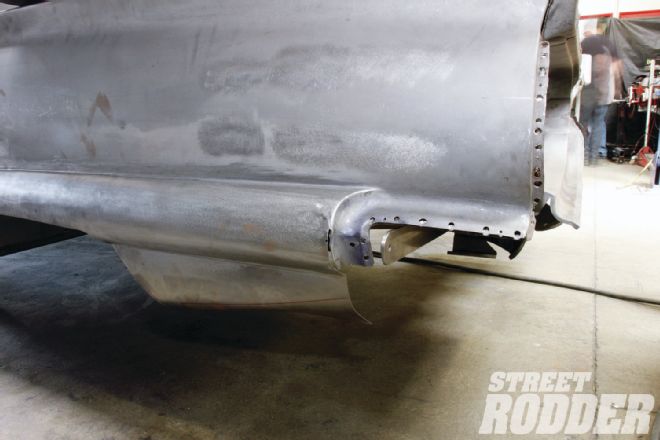
16. This driver-side custom panel shown in photos 7 and 8 has been welded in place and metal finished. Work has started on bending the lower portion to curve under.
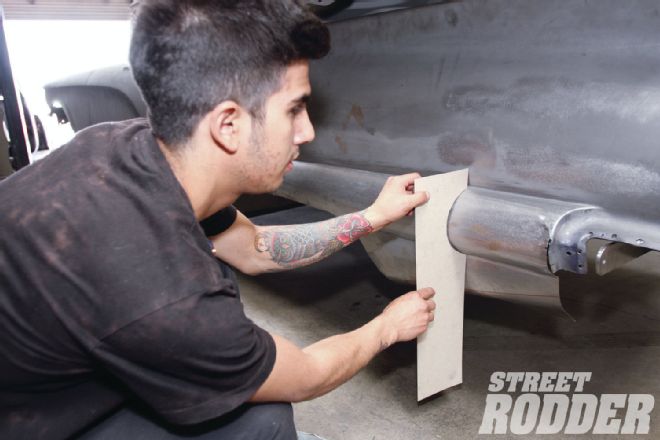
17. A cardboard template will ensure that the spear shape is identical on both sides of the car.
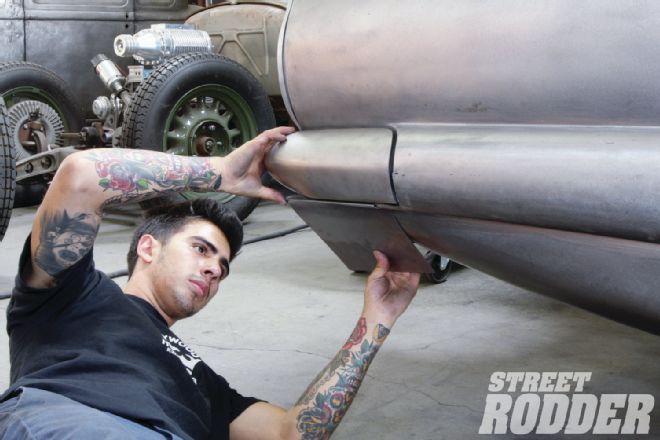
18. On the passenger side, the curve of the lower rear quarter has been created. The bottom of the bumper has been cut to continue the lines of the spear, and sheetmetal is being added to extend the body below the bumper, for a finished-flowing appearance. The 90-degree angle at the lower corner of the bumper will be radiused to match the top.
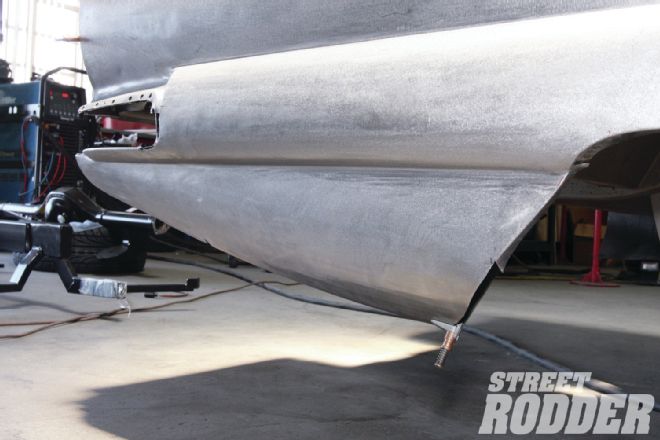
19. The lower quarter now extends completely to the rear where it curves below the bumper.
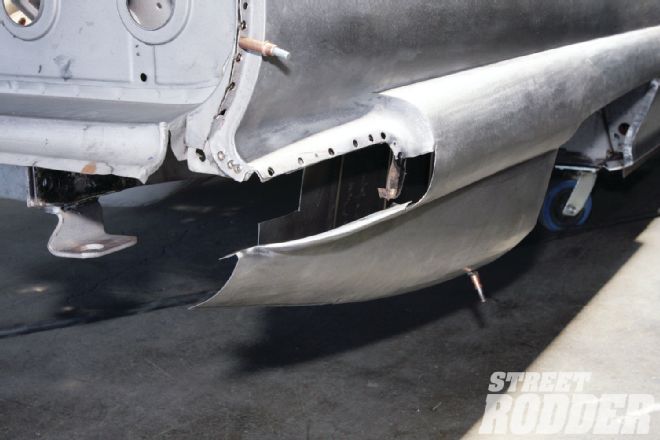
20. The rear of the spear has been radiused.
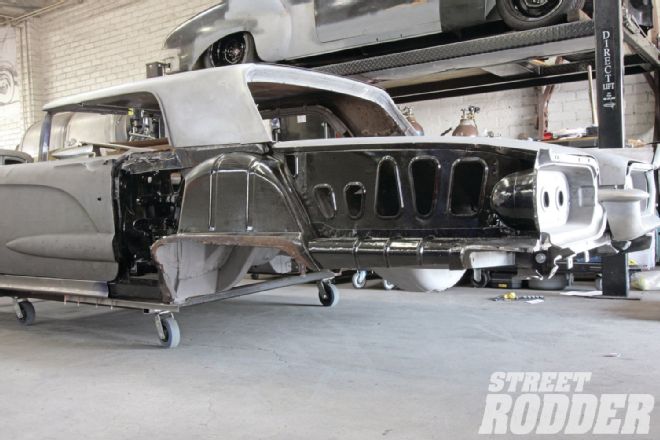
21. Because the quarter-panels were reshaped and extend much lower than the originals, part of the inner structure had to be removed and rebuilt from scratch for support.
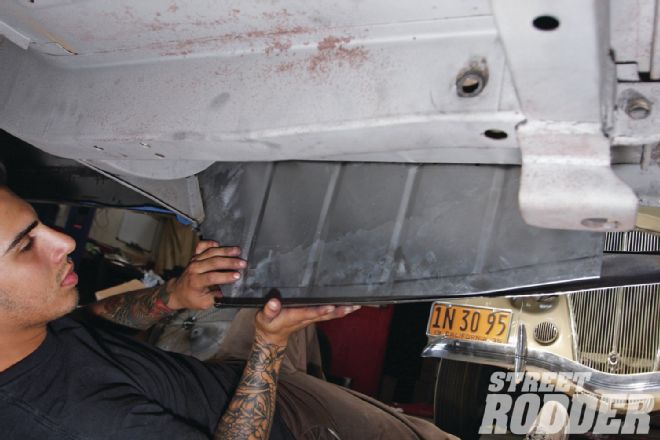
22. Continuing to remove the original structure.
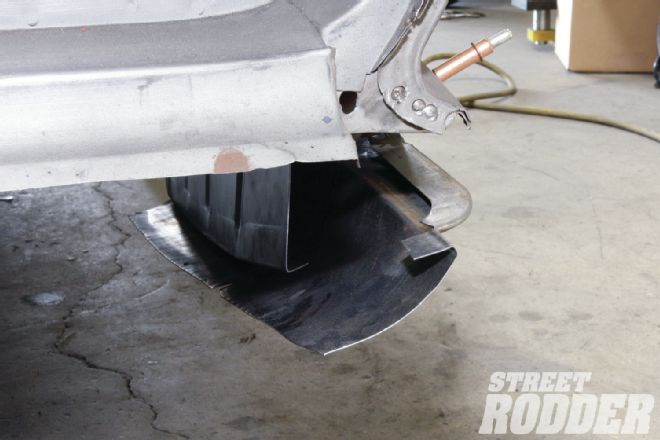
23. These scratch-built inner structures box the new lower panels. The lower quarter will be trimmed and the two pieces will be welded.
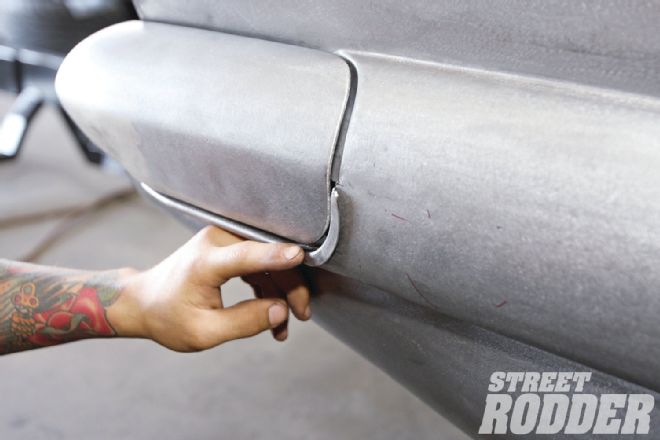
24. Radiusing the bumper left a gap in the corner that was filled by fabricating and a small crescent to be welded in place.
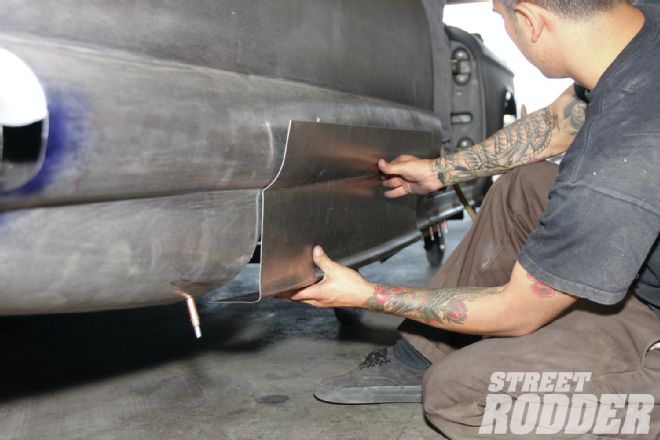
25. Custom fender skirts were fabricated, extending vertically from the lower section of the spear and continuing the lower body lip. The skirt was curved to follow the body shape using an English wheel.
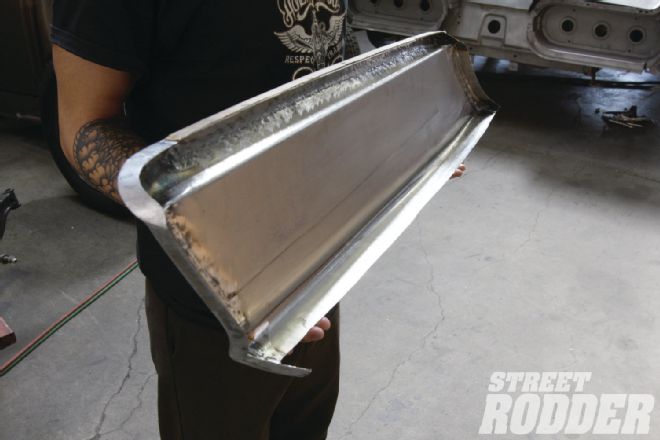
26. The skirts were fabricated with a 3/4-inch flange to fit flush within the wheel opening.
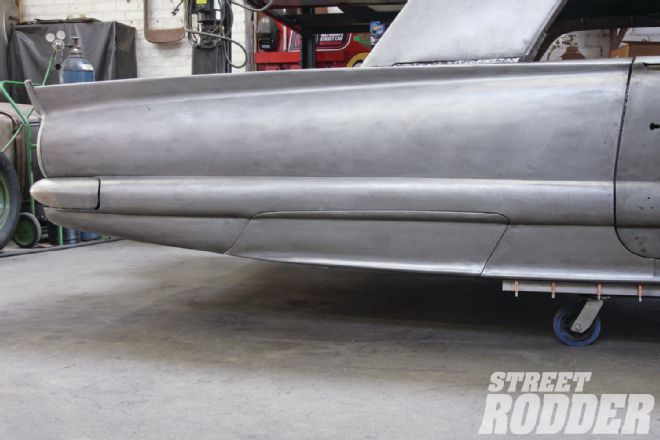
27. The finished skirts are held in place with spring-loaded latches at the front and rear, and positioning pins along the top, just like the flush-fit ’51 Mercury skirts highlighted in the Apr. ’13 issue of STREET RODDER.
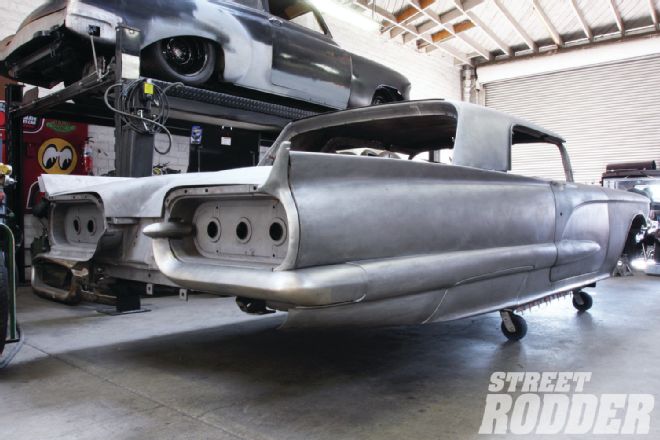
28. With the full-length spear, flush-fit skirt, taillight bezel, and shaved bumper in place, you get the full effect of one portion of the extensive modifications in store for the T-bird.