Check out Part 1 and Part 2 of this series on building the next generation race engine!
Welcome back to Circle Track’s continuing experiment to see how an engine based on LS7 architecture will work as a full-bore dirt racing engine. Yes, Chevrolet Performance does sell the LS-based CT525 crate engine, and it is a great option for crate racing. But we know this engine design is capable of so much more, especially thanks to ever growing aftermarket support. And besides, why settle for a “mere” 525 horsepower when you can shoot for 600 or more?
1. In case you missed it in one of our earlier articles, there are plenty of differences between the LS design and the tried-and-true Chevy small-block you are already used to. The deep skirted block and cross-bolted main caps (the ones from RHS are high strength billet steel) may look different, but the thrust bearing is in the same place and the same bearing clearances that work well with a first-generation small block will work well here, too.">

<strong>1. </strong>In case you missed it in one of our earlier articles, there are plenty of differences between the LS design and the tried-and-true Chevy small-block you are already used to. The deep skirted block and cross-bolted main caps (the ones from RHS are high strength billet steel) may look different, but the thrust bearing is in the same place and the same bearing clearances that work well with a first-generation small block will work well here, too.
2. Bob Cronin, owner of CRD Engine Development, says he uses Calico’s coated bearings in his builds because he trusts their repeatability and the quality of the lubricating coating. It’s hard to argue with success—CRD’s LS engines have won multiple sports car racing championships—so we ordered up a sets of Calico’s main and rod bearings for this build as well.">

<strong>2. </strong>Bob Cronin, owner of CRD Engine Development, says he uses Calico’s coated bearings in his builds because he trusts their repeatability and the quality of the lubricating coating. It’s hard to argue with success—CRD’s LS engines have won multiple sports car racing championships—so we ordered up a sets of Calico’s main and rod bearings for this build as well.
3. Cronin checked the bearing clearances on our 4.000-inch stroke Lunati forged crank with Calico bearings in the housing bores and got 0.0023-inch of clearance.">

<strong> 3. </strong> Cronin checked the bearing clearances on our 4.000-inch stroke Lunati forged crank with Calico bearings in the housing bores and got 0.0023-inch of clearance.
4. In addition to Cronin, Rick Fred is one of CRD’s lead engine builders, and we were grateful when he pitched in on our build as well. While Cronin measured up the main bearing clearances, Fred began assembly of the rods and pistons.">

<strong>4. </strong> In addition to Cronin, Rick Fred is one of CRD’s lead engine builders, and we were grateful when he pitched in on our build as well. While Cronin measured up the main bearing clearances, Fred began assembly of the rods and pistons.
5. When choosing a coated bearing, make sure the bearing beneath it is also high quality. In this case Calico is using Mahle Clevite’s performance bearings as the foundation for its protective coatings.">

<strong> 5. </strong> When choosing a coated bearing, make sure the bearing beneath it is also high quality. In this case Calico is using Mahle Clevite’s performance bearings as the foundation for its protective coatings.
6. The rod bearings measured out with a consistent clearance of 0.0025-inch.">

<strong> 6. </strong> The rod bearings measured out with a consistent clearance of 0.0025-inch.
7. Finally, Cronin is ready to lay the crank into position. The LS design uses a one-piece rear main seal that mounts into a rear plate, so sealing the engine isn’t a concern at this point.">

<strong>7. </strong> Finally, Cronin is ready to lay the crank into position. The LS design uses a one-piece rear main seal that mounts into a rear plate, so sealing the engine isn’t a concern at this point.
8. For maximum strength, RHS utilizes ARP studs in the block as well as ARP fasteners for the cross bolts. When torquing the main caps in place, begin with the center studs and work your way outward with the cross-bolts the final step. Using the included ARP thread lubricant, torque the studs to 90 lb-ft and the cross bolts to 35.">

<strong>8. </strong>For maximum strength, RHS utilizes ARP studs in the block as well as ARP fasteners for the cross bolts. When torquing the main caps in place, begin with the center studs and work your way outward with the cross-bolts the final step. Using the included ARP thread lubricant, torque the studs to 90 lb-ft and the cross bolts to 35.
9. The rest of the rotating assembly will be Mahle forged and coated pistons hung on 6.125 forged Lunati I-beam connecting rods.">

<strong> 9. </strong> The rest of the rotating assembly will be Mahle forged and coated pistons hung on 6.125 forged Lunati I-beam connecting rods.
In previous installments of this engine build we took a closer look at the major components and why we chose them, and we also documented engine builder Bob Cronin’s pre-fitting process. This time around we are finally putting parts together, and we’re happy to sit back with a Coke while CRD Engine Development’s own Cronin and Rick Fred does all the work. While Fred was assembling our short block, we could hear some of CRD’s LS-based sports car racing engines wailing on the facility’s two dyno cells, and we can’t wait to hear this 400-plus-inch bad boy fired up for the first time.
This engine design is capable of so much more, especially thanks to aftermarket support
10. Instead of spiral pin locks, the Mahle pistons use a round wire lock that still securely locks the piston’s wristpin in place but can’t wear the groove in the pin bore. Fred presses them expertly in place using a small screwdriver.">

<strong>10. </strong>Instead of spiral pin locks, the Mahle pistons use a round wire lock that still securely locks the piston’s wristpin in place but can’t wear the groove in the pin bore. Fred presses them expertly in place using a small screwdriver.
11. In order to squeeze that extra long 6.125 connecting rod as well as a 4.000-inch stroke crank into a standard deck block the compression height on the pistons has to be quite short. So short, in fact, that the pin bore intrudes into the oil ring groove. To fix this, an oil ring support rail must be installed before the oil ring components. The support rail can’t be allowed to spin, or else the ring gap can wind up over the opening in the groove. The support rail has a dimple that must be situated so that it faces downward over the opening created by the pin bore once the ring is installed. This keeps the rail from spinning.">

<strong>11.</strong> In order to squeeze that extra long 6.125 connecting rod as well as a 4.000-inch stroke crank into a standard deck block the compression height on the pistons has to be quite short. So short, in fact, that the pin bore intrudes into the oil ring groove. To fix this, an oil ring support rail must be installed before the oil ring components. The support rail can’t be allowed to spin, or else the ring gap can wind up over the opening in the groove. The support rail has a dimple that must be situated so that it faces downward over the opening created by the pin bore once the ring is installed. This keeps the rail from spinning.
12. Once the support rail is in place, the oil ring package can be installed just like normal.">

<strong>12. </strong>Once the support rail is in place, the oil ring package can be installed just like normal.
13. Fred carefully installs the first and second rings. The ring package is supplied by Mahle and is a lightweight 1.5/1.5/3.0 millimeter set for minimum drag. The top rings have already been gapped to 0.0018-inch while the second rings have a cold gap of 0.0016.">

<strong>13. </strong>Fred carefully installs the first and second rings. The ring package is supplied by Mahle and is a lightweight 1.5/1.5/3.0 millimeter set for minimum drag. The top rings have already been gapped to 0.0018-inch while the second rings have a cold gap of 0.0016.
14. Finally, Fred is ready to install the freshly completed piston and rod assemblies into the block. The LS block numbers the cylinder bores just like a traditional small block.">
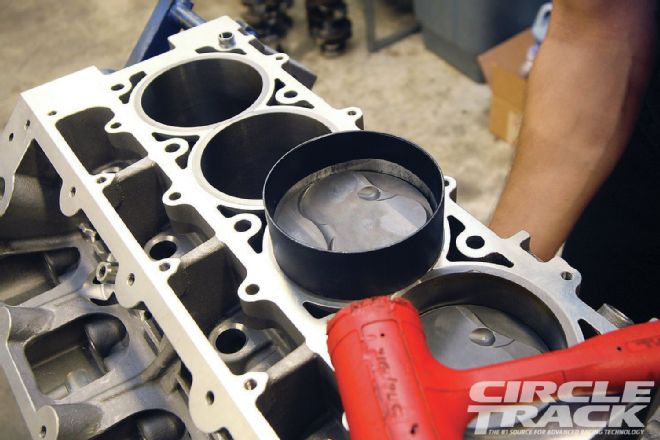
<strong>14. </strong>Finally, Fred is ready to install the freshly completed piston and rod assemblies into the block. The LS block numbers the cylinder bores just like a traditional small block.
15. Fred installs the rod caps and finger tightens the bolts until all the pistons are in the bores.">

<strong>15. </strong>Fred installs the rod caps and finger tightens the bolts until all the pistons are in the bores.
16. All the rod bolts are installed with ARP’s Ultra Torque lubricant and stretched to 0.0055-inch to ensure maximum clamping without over-torquing the fasteners.">

<strong>16. </strong>All the rod bolts are installed with ARP’s Ultra Torque lubricant and stretched to 0.0055-inch to ensure maximum clamping without over-torquing the fasteners.
17. The short block is complete and ready to go. Next time around we’ll install the valvetrain Comp Cams has put together specifically for this application. ">

<strong>17. </strong>The short block is complete and ready to go. Next time around we’ll install the valvetrain Comp Cams has put together specifically for this application.